As other businesses shift to skeleton crews, the cold chain industry is up and running faster than ever before. Lowell Randel, VP of government and legal affairs for the Global Cold Chain Alliance (GCCA) sated in an interview with Supply Chain Dive, “I think just fundamentally, the supply chain is very resilient, and our members and their customers are very, very resilient.” He goes on to say that many food producers have adjusted production lines, which could mean a different mix of products, or switching to full pallets that can be moved more efficiently than individual cases.
However, shifts in production or low temperatures are no match for reliability or productivity with the right tools in place. Now more than ever, it is vital for cold chain environments to be leveraging every possible second to its fullest extent. In fact, Randel stated that staples including meat, poultry, eggs and dairy have been in particular demand. A recent study by Nielson shows that fresh meat sales are up 48% for the week ending March 14th over the same period last year and poultry is up 52%.
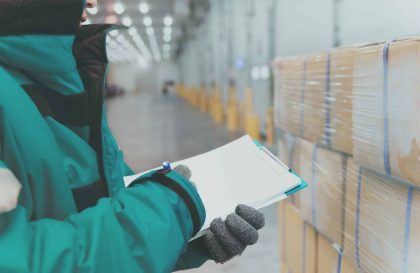
This has lead to what Randel states as the “…biggest misconception (during COVID-19) is that empty grocery shelves are an indicator that there is a shortage of food. The recent runs on grocery stores have created short-term disruptions as the supply chain works to catch up and replenish stocks…the supply chain itself is strong and working.”
Workers in the cold chain play a critical role in ensuring the nation’s food supply is met during the best—and sometimes during the most challenging—of times. To help support frontline workers and your operation, here are four tips for maximizing efficiencies in cold chain environments.
Streamline Cold Storage and Handling
Low temperatures don’t need to be the culprit of reduced reliability or productivity. But what they do require is specialized equipment to streamline the handling and tracking of products through the supply chain. A standard model supply chain mobile computer just won’t cut it for prolonged use within cold environments. However, manufacturers have adapted and incorporated heaters as well as specialized housing, components and peripherals to set cold chain devices apart from standard models.
For example, the Honeywell CK65 freezer model mobile computer has all of the state-of-the-art functionality as the standard model with the addition of being capable of operating in temperatures of -22 degrees Fahrenheit with integrated heaters, higher Ingress Protection (IP) ratings, multi-shift battery life, glove friendly keypads, and FlexRange scanners to improve accuracy in extreme conditions regardless of type of barcode.
Another option is the Zebra MC9300 Freezer handheld computer, which is a staple of Zebra’s cold chain mobility portfolio, capable of operating in extreme temperatures, and with specialized features including heated scanner exit window, freezer-rated battery, and zero condensation.
Assess Wireless Networking
The most modern mobile devices could be challenged to perform optimally if the wireless networking within your supply chain environment is not up to par. It is critical for access points (APs)to be installed directly in refrigerated or frozen storage areas to provide proper coverage.
Relying on APs outside the cold zone will result in weak and blocked signals because of the interference of thick walls and insulation. This means that APs within the freezer environment require specialized heated enclosures to protect against condensation and cold. Specialized antennas with common access points are also ideal in order to correct the multipath effect prone to cold environments with heavy condensation. If your operation isn’t experiencing rock-solid WLAN, a wireless site assessment will help—and there are providers who are troubleshooting wireless networking remotely during COVID-19.
Consider Alternative Data-Collection Options
Consider using speech recognition and RFID alternatives to increase accuracy in data entry within your cold chain environment. Speech recognition terminals can be worn on a belt or holster and worn under coats where they aren’t exposed to cold temperatures. In fact, a recent report showed that nearly 1 million DC workers using Honeywell voice-directed solutions have achieved 35% productivity gains, 50% error reductions, and 30% fewer safety incidents.
The benefit of leveraging RFID to collect data is that it requires no line of sight. As condensation frequently occurs after pallets are shrink wrapped, it can be challenging for laser devices to read labels underneath, where RFID will be able to read data accurately and efficiently.
Don’t Leave Workers Out in the Cold
Cold chain employees are ahead of the curve when it comes to complying to excellent hygiene standards including hand washing, appropriate PPE, regular cleaning of work surfaces and machinery. However, COVID-19 presents the need for increased precautions and protection against the airborne droplets that spread infection. In addition to practicing social distancing, facemasks, physical segregation barriers and no touch hand sanitizers in high trafficked areas are vital protocol to protecting employees and the integrity of the supply chain.