Barcode label printing is part of a cost-effective barcode system that allows businesses to manage inventory, track assets, and maintain efficient supply chain operations. For small-to-midsize businesses looking to implement barcoding for the first time, or make existing barcode printing operations more efficient, choosing the right barcode printer for your application will prevent headaches, improve reliability, and avoid unnecessary spending.
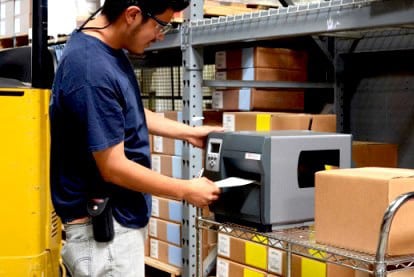
Here is a quick checklist of things to look for and recommendations to ensure you get the most out of your labeling solutions:
- Extending Printhead Life With the Right Ribbon – The cost of a printhead is an often overlooked piece of the on-demand printing solution, usually running between $500 and $1000 dollars for each one. So would it surprise you if ribbons and labels you chose in order to save money end up costing you more because they might damage the printhead? Always use quality ribbons that have protective backcoatings which help to keep the printhead from getting scratched or abraded during printing.
- Optimizing Your Supply Chain – Where print volumes are high and variable due to seasonality, label supply and inventory becomes challenging. Carrying an overabundance of labels or ribbons in inventory is not desirable, but nor is having a shortage at a critical time and having to wait for shipping. It’s best practice to work with a provider offering multiple buying options like “Blanket Orders”, “Min-Max” or “Make and Hold”. Programs like these let the customer receive consumables when they need them and helps to avoid stock outs. In addition, top tier providers will have facilities or manufacturers in place in multiple regions to minimize the shipping time and cost to reach you when you are ready for replenishment, and will also offer “kitting” (putting labels and ribbons in the same box, using one part number to ensure proper pairing when re-ordering).
- Putting the Right Ribbon to the Right Paper – Trying to get the ink type correct means the surface characteristics of the face sheet must be considered. For applications using general-purpose paper label applications a wax ribbon is usually recommended. But if you require more durability or the substrate (the surface where the label is being applied) is a mid-range synthetic like polypropylene then a wax/resin ink is best. For a harsher environment like cold storage or outdoor application, using a polyester or similar label would require a full resin ink instead. However, each application has its unique aspects which may require a specific ribbon, so again it is recommended to consult with a qualified vendor and conduct sampling as well.
- Match the Label to Your Processes – It’s not just about the environment, but also how the label interacts as part of your process. And the specifics matter. For example, “scanning barcodes” seems basic, but “scanning barcodes from more than a few feet away” means you will need an entirely different label (in this case, a “retro-reflective” material which will enable scanning up to 20 feet away – ideal for use when working from aisle pickers and with high bays or taller racks).
- Include the Label Process in Your Floor Training – A common failure point of labels is when they are applied by hand on the floor, where incorrect application can be a leading cause of the label falling off the product or package. This is the worst case scenario for outbound product shipments, as it means both a lost product and potentially a lost customer as well. For example, labels should always be applied by pulling the liner away from the label, not the other way around. If the label is pulled away from the liner then it will impart curl and could lift during the application or be prone to lift later where it might get torn off on a conveyor or sorting machine.
- Labels not Scanning at Farther Distances – When we have to scan labels at distances greater than a couple of feet, there are materials called “retro-reflective”, which enable users to scan at distances up to 20 feet or more. These labels are often used in warehouse applications where labels are up high on racks.
Get The Experts To Take A Look
These are just a few of the many tips and best practices out there when it comes to perfecting your label solution. For optimal results, fewer errors and happier customers, consult with a qualified label expert to ensure you have the optimal label solution for your application.
Continue Reading
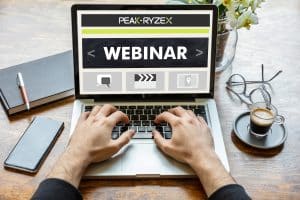
Maximizing Order Fulfillment Performance with AI-enabled Drones
Watch Now: Maximizing Order Fulfillment Performance with AI-enabled Drones Join industry leaders from Peak Technologies, Gather AI, and Barrett Distribution Centers to discover how cutting-edge
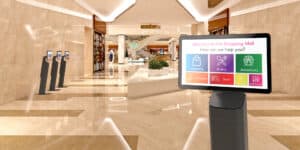
The Phygital Revolution: Blending Physical and Digital Retail Experiences
The retail landscape is undergoing a profound transformation, driven by the convergence of physical and digital experiences, a phenomenon known as the “phygital revolution.” This
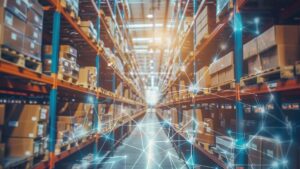
What is Supply Chain ESG & What is the Impact?
ESG has attracted a lot of attention in recent years, but remains poorly understood, not to mention, underutilized by the many organizations that stand to
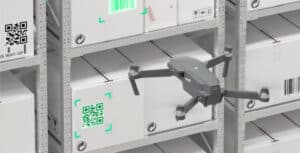
How Drones Are Transforming Warehouse Inventory Management and Tracking
Robotics and artificial intelligence promise to transform the warehouse environment, offering exciting new opportunities to optimize inventory management. These advancements are just the start of
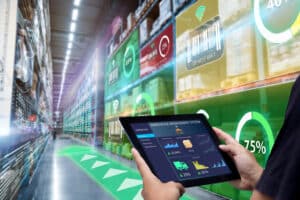
The Role of Smart Technologies in Warehouse Sustainability
Sustainability is a growing trend in warehousing, and for good reason: today’s consumers expect that the companies they support will show an authentic commitment to
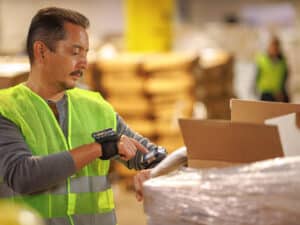
Emerging Trends in Supply Chain and Warehouse Technologies
The modern warehouse is an innovative powerhouse, driven by a fascinating array of tools and technologies that promise a new vision of supply chain success: