About the Company
Henry Schein, Inc., the world’s largest provider of health care products and services to a wide variety of medical offices, needed a wireless mobile computing solution that could handle more product flow without adding labor.
When Henry Schein, Inc., used a paper-based process to manage the flow of goods, a considerable proportion of its staff’s time was occupied with data entry and handing paper. Now, thanks to Peak Technologies, a wireless mobile computing system that interfaces with the company’s enterprise resource planning (ERP) system automates the record-keeping involved in the unloading, receiving, put-away, and cycle counting operations.
Business Challenge
Henry Schein, Inc. needs to prepare nearly all orders received by early afternoon for same-day shipment. The service is designed to provide customers located in a one-day ground delivery zone from any of its warehouses with next-day delivery at no extra cost. Meeting these requirements using the company’s previous paper-based distribution methods was a very tedious process. At each stage of the process, workers had to fill out paper forms that were later delivered to clerks and keyboarded into the ERP system. Consequently, a high proportion of staff time was occupied by data entry and handling the paper documents.
Another problem was errors inevitably made in filling out the forms and entering the information into the system. In order to maintain high levels of accuracy, the company had to maintain an extensive auditing process that double-checked nearly every document and data entry process. Finally, the documentation associated with each order, such as the invoice, shipping list and material safety data sheets, all came from different systems at different points in the process. This meant another tedious manual process was required to assemble the proper documentation for each order prior to shipment and made it impossible, in most cases, to provide the customer with the invoice as part of the shipment.
The Solution
Based on Peak Technologies’ strengths and expertise in all areas of wireless and mobile computing technology, Henry Schein, Inc. went with a new solution that begins when a truck pulls up to the loading dock. The receiver scans with paperwork with the Zebra mobile computer and the items are immediately entered into inventory. As the items are scanned, a work order is generated for the receiver that tells the worker exactly where each item should be taken – and calls out any items that have a special priority because they are needed to fill existing orders. Consequently, items are on the shelf quickly and available for filling customer orders as soon as possible..
The receiving team opens the packages and breaks them down by location. Put-away labels are automatically printed by a thermal printer in the receiving area. The loader then takes the merchandise to the correct location in the warehouse and scans both the location and merchandise labels. When the labels are scanned, the system checks to be sure the merchandise is being put into the right spot. If not, it calls out the error to the operator. When the merchandise is correctly put away, the product immediately appears as being available for sale in the ERP system.
Featured Product
- Zebra Mobile Computers
- Zebra Barcode Printers
Featured Peak Technologies Services
- Wireless Site Surveys
- Wireless Infrastructure Design Services
- Wireless Implementation Services
- Training
- Go-Live Support
The Results
The Peak Technologies wireless mobile computing solution has reduced the time from when merchandise is received at the dock to when it is available for sale from one-and-a-half days to about three hours. Inventory control operations, cycle counting and sweeping have also been substantially improved. Sweeping, it should be noted, is similar to cycle counting except that it proceeds location-by-location rather than product-by-product. In the past, these operations had to be done during the working day because that was when the inventory information in the ERP system was the most accurate. Consequently, people performing these operations often interfered with and slowed the work of the operators performing put-away and picking operations. With the wireless mobile computing system, staff have been moved to higher value-added jobs that involve moving products and customer contact. The results include:
- Accommodating sales increases averaging 28 percent per year over the past eight years without increasing distribution center staff
- Fill rate, order accuracy and same-day ship rates all at 99.7 percent or higher
- Inventory entries made on a near-real-time basis
- Counting operations can be performed during less busy evening hours
- Productivity is increased by eliminating manual paper forms and data entry errors
- Faster assembly of shipping documentation
- Eliminates purchasing and stocking of special forms
- Enables documents to be customized to include invoice shipment or other customer requests
Download the PDF Version
Click the download button below to download the PDF version of this case study to save or share.
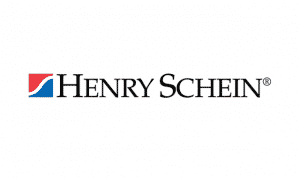
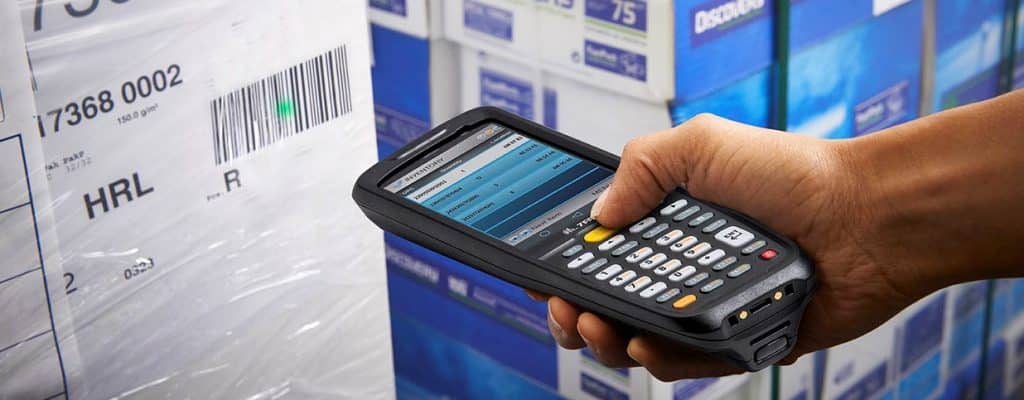
Industry:
Wholesale Distribution
Business Challenge:
Eliminate Paper-based Processes from Distribution Center Operations
Location:
Northeastern United States
Featured Product:
- Zebra Mobile Computers
- Zebra Barcode Printers
Featured Peak Technologies Services:
- Wireless Site Surveys
- Wireless Infrastructure Design Services
- Wireless Implementation Services
- Training
- Go-Live Support
"The Peak Technologies wireless mobile computing solution has reduced the time from when merchandise is received at the dock to when it is available for sale from one-and-a-half days to about three hours.”